What is Cold Drawing?
Cold drawing is a fascinating manufacturing process that has revolutionized how we shape and refine materials. However, unlike other methods, cold drawing is performed at room temperature, which brings a host of benefits to the table.
Below, we’ll break down what cold drawing is all about, why it’s important, and how it compares to other drawing processes. Let’s dive into it!
Definition of Cold Drawing
First, let’s examine the definition of cold drawing. In simple terms, cold drawing is a metalworking process in which a metal rod, wire, or tube is pulled through a die to make the cross-sectional area smaller.
This technique is called "cold" drawing because it is done at room temperature rather than being heated, like with “hot drawing.” The result? The material's strength and hardness improve, along with its surface finish and dimensional precision.
Importance of Cold Drawing in Manufacturing Processes
So, why exactly is cold drawing so important in the manufacturing process? Well, it allows for the precise control of material dimensions and properties.
This accuracy is vital in industries where tight tolerances and high performance are required, such as in the production of aerospace components, or automotive parts.
Cold Drawing Process
Explanation of the Cold Drawing Process
The cold drawing process begins with the selection of a suitable raw material, usually a wire, rod, or tube. This material is then lubricated to reduce friction and pulled through a die, a tool with a precisely sized hole.
As the material is drawn through the die, its diameter is reduced, and its length is increased. This action refines the material's grain structure, enhancing its strength and durability.
Comparison with Other Drawing Processes
Cold drawing stands out from other drawing processes like hot drawing and plastic drawing due to its temperature and resulting material properties. Hot drawing involves heating the material to make it more pliable, which can be beneficial for certain applications but often results in a less precise finish.
Plastic drawing, on the other hand, is used for polymers and other non-metallic materials. Cold drawing offers superior surface finish, tighter dimensional tolerances, and improved mechanical properties compared to these other methods.
Benefits of Cold Drawing
Cold drawing offers several benefits, some of which you may not be aware of. Let’s take a look at them below:
- It significantly enhances the material's strength and hardness without compromising its ductility.
- The process also improves the surface finish, making the final product smoother.
- Cold drawing allows for tighter dimensional tolerances, ensuring that components meet exact specifications. This precision is especially crucial in industries where reliability and performance are important.
Next, we’ll take a look at what materials are used in cold drawing.
Materials Used in Cold Drawing
Selection of Materials for Cold Drawing
Picking the right materials for cold drawing is all about what you need from the finished product. Steel, copper, aluminum, and their various alloys are the go-to choices because they can handle the stress of the drawing process. They also offer specific mechanical properties once drawn.
Influence of Material Properties on the Cold Drawing Process
The properties of the material being drawn are crucial in determining how the process will go. Factors like tensile strength, ductility, and hardness play a big role in how the material behaves during drawing and what kinds of products you can make.
For example, high-strength steels are perfect for parts that need to be super durable, while you may choose copper and aluminum for their conductivity and how lightweight they are.
Examples of Materials Commonly Cold Drawn
Steel is probably the most commonly cold-drawn material due to its strength and versatility. Copper is another favorite, especially in the electrical and plumbing industries, thanks to its high levels of conductivity and corrosion resistance.
Aluminum, known for being lightweight and corrosion-resistant, is also frequently cold-drawn, making it a staple in the aerospace and automotive sectors.
Equipment and Tools Used in Cold Drawing
Description of Drawing Machines and Their Components
Cold drawing requires some pretty specialized gear to get those precise results. Drawing machines typically include a die, a drawing bench, and a lubrication system. The die shapes the material, while the drawing bench provides the pulling force needed. Modern machines are often automated, which helps ensure consistent, high-quality production.
Role of Lubricants in the Cold Drawing Process
Lubricants are essential in the cold drawing process because they reduce friction between the material and the die, preventing damage and ensuring a smooth surface finish. The type of lubricant you use can make a big difference in the final product's quality. Effective lubrication also helps extend the life of the die and the drawing machine, making the whole operation more efficient.
Importance of Manufacturing Tools for Cold Drawing
The quality of the tools you use in cold drawing matters. For example, the die and drawing bench are crucial to achieving the desired results.
High-precision tools ensure the material is drawn accurately, maintaining tight tolerances and a high-quality finish. Regular maintenance and carefully selecting these tools are essential for keeping everything running smoothly and extending the equipment's lifespan.
Applications of Cold Drawing
Industries That Utilize Cold Drawing
Cold drawing is a big deal across various industries because it produces high-quality, precise components. Key players include the automotive, aerospace, construction, medical, and electronics sectors. Each of these industries relies on the unique benefits of cold-drawn materials to meet their specific needs.
Examples of Products Created Through Cold Drawing
You’ll find cold drawing at work when making everything from tubing and wires to bars. For example, cold-drawn steel is used for components like axles and gear shafts in the automotive industry. The construction industry uses cold-drawn reinforcing bars to build strong, durable structures. And in electronics, cold-drawn copper wire is crucial for efficient electrical transmission.
Advantages of Using Cold Drawing in Manufacturing Processes
Cold drawing has tons of advantages in manufacturing. It allows for the production of components with superior strength and precision, which are essential for high-performance applications. Plus, it enhances the surface finish, reducing the need for additional processing. The process is also highly efficient and cost-effective, making it a top choice for large-scale production.
Challenges and Considerations in Cold Drawing
Impact of Temperature on the Cold Drawing Process
Even though cold drawing is done at room temperature, friction can generate significant heat. Managing this heat is crucial to prevent material degradation and keep the drawing tools in good shape. Proper lubrication and cooling systems are key to controlling temperature and ensuring consistent quality.
Tensile Strength and Wall Thickness Requirements
For many people, getting the right tensile strength and wall thickness in cold-drawn materials can be tricky. The process needs to be carefully controlled to meet specific requirements. This involves selecting the appropriate raw material, optimizing drawing parameters, and maintaining precise control at all times.
Dimensional Tolerances and Surface Finishes
Maintaining tight dimensional tolerances and achieving a high-quality surface finish is critical in cold drawing. Any deviations can impact the performance and reliability of the final product. Regular inspection and quality control measures are necessary to ensure that drawn materials meet the required standards.
Addressing Internal Stresses and Deformation
Cold drawing can introduce internal stresses and deformation in the material, which need to be addressed to ensure the final product's integrity. Annealing, a heat treatment process, often relieves these stresses and restores the material's flexibility. Proper handling and post-processing are essential to maintain the desired properties of the drawn material.
Advancements in Cold Drawing
Introduction of Automated Cold Drawing Processes
Automation has brought significant advancements to the cold drawing process. Automated systems allow for precise control of the drawing parameters, resulting in consistent quality and increased production efficiency. These systems also mean less manual intervention and minimize the risk of errors, thus improving workplace safety.
Improved Surface Finish Techniques
New techniques for improving the surface finish of cold-drawn materials help enhance the final product's overall quality and appearance. Advanced polishing and coating methods reduce surface imperfections and increase corrosion resistance, extending the lifespan of the components.
Development of New Materials for Cold Drawing
Ongoing research and development have led to the creation of new materials specifically designed for cold drawing. They offer increased strength, improved flexibility, and better resistance to wear and corrosion.
How Drawn Metal Can Help
At Drawn Metal, we specialize in providing high-quality cold-drawn materials for a range of applications. Whether you require precision tubing, robust wires, or custom-shaped bars, you can find everything you need.
If you have any enquiries, you can contact us for more information. You can also browse our range of products on our website.
Contact Us Today!
Download our DMT Brochure
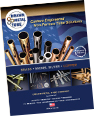