What is Deburring?
Deburring plays a key role in the metal manufacturing process. Whether you’re in the automotive industry, aerospace, or general manufacturing space, deburring maintains the safety, functionality, and aesthetic quality of machined parts.
But what exactly is deburring, and why is it so essential? Below, we'll take a look at the concept of deburring, the formation of burrs, the different methods of burr removal, and the importance of this process in machining.
What Is a Burr, and How Can It Impact Machining?
A burr is a rough edge or small, unwanted piece of material which stays attached to your metal product after a machining process such as milling, drilling, or cutting. These imperfections are often tiny but sharp and can affect both quality and functionality.
While small, these burrs can lead to a range of issues. For example, they can compromise the aesthetic appearance of the part and cause mechanical failures. In some cases, burrs can even interfere with the assembly process, leading to increased production costs and potential safety hazards, particularly in critical industries like automotive manufacturing.
What Causes a Burr?
Burrs are typically the result of various factors during the machining process. If you can develop an understanding of what causes these burrs, you can help to minimize their formation.
- The Operator's Proficiency: The skill level of the machine operator plays a significant role in the formation of burrs. Inexperienced or less proficient operators may not correctly set the cutting parameters, such as feed rate, tool speed, and depth of cut, leading to increased burr formation. However, using Numerical Control (NC) or Computer Numerical Control (CNC) machines can help reduce operator error by automating the machining process. This should give you more consistent results.
- Grade and Thickness of the Material: The type and thickness of the material being machined also significantly influence burr formation. For instance, softer metals like aluminum are more prone to burrs compared to harder metals like steel. Additionally, thinner materials are more likely to produce burrs as they are easier to deform during the cutting process. Even materials like plastic can develop burrs, particularly when using high-speed machining or when the material is prone to melting under heat.
How Does A Deburring Machine Work?
Deburring machines are specialized tools designed to remove burrs efficiently and consistently from various types of materials. They work via one or more of the following principles:
- Abrasive Action: Many deburring machines use abrasive belts, brushes, or wheels to physically grind or sand away burrs. The part is passed through the machine, where the abrasive material removes the unwanted edges. The machine’s speed, pressure, and type of abrasive used can be adjusted depending on the material and the amount of deburring required.
- Rotational and Vibrational Movement: Some deburring machines use rotational or vibrational motion to remove burrs. For example, in vibratory deburring, the parts are placed in a vibrating chamber filled with abrasive media. The vibration will make the media to grind against the parts, which helps to smooth the burrs. You’ll find this method is particularly effective for small parts and components with complex shapes.
- Heat and Chemical Action: Thermal deburring machines utilize controlled explosions to generate heat, which burns off burrs. This process is particularly effective for internal burrs that may be otherwise difficult to reach. Similarly, electrochemical deburring machines use an electrolytic solution and electrical current to dissolve burrs, so it’s useful if you need to make precision parts.
- Automation and Precision: Modern deburring machines are often equipped with CNC controls, allowing for high precision and consistency. You can program it to perform specific deburring tasks with minimal human intervention. This will help you to reduce the chance of operator error and ensure uniform results across multiple parts.
The choice of deburring machine depends on various factors, including the material being worked on, the size and complexity of the parts, and the desired finish. Whether you're dealing with metal, plastic, or other materials, using the correct one can significantly improve both the quality and performance of your metals.
How Do You Remove Burrs From Metal?
Removing burrs will help your final product meet quality standards and functions as you intended. So, how exactly do you remove burrs from metal? We’ll break down several different metals below to help you remove burrs from metal, each with its own advantages and applications. Here’s a look at the most common deburring techniques:
Mechanical Deburring
Mechanical deburring is one of the most traditional methods you can use to remove burrs. This process involves physically grinding, sanding, or filing away the burrs using various tools and machinery. If you need to remove larger burrs, then this is a good process to use in conjunction with other deburring methods.
However, mechanical deburring can be labor-intensive. As a result, it may not be suitable for any highly complex or delicate components you want to produce.
Thermal Deburring
Thermal deburring, or "thermal energy method" (TEM), is where you use controlled explosions to burn away burrs. The workpiece is placed in a chamber filled with a combustible gas mixture.
When ignited, the heat generated by the explosion burns off the burrs while leaving the rest of the component intact. This method is useful if you want to remove burrs from hard-to-reach areas and internal passages, but it requires specialized equipment and safety precautions.
Electrochemical Deburring (ECD)
Another way to remove burrs from metal is via electrochemical deburring (ECD). This is a precision deburring technique that uses an electrolytic solution and electrical current to remove burrs.
The process is highly controlled and ideal if you want to remove burrs from complex geometries or delicate parts without affecting the material’s overall integrity. It’s also particularly useful for parts with intricate details, where other deburring methods might not be as effective. For example, the automotive industry where precision is needed may use this process.
Cryogenic Deburring
Removing burrs using cryogenic deburring involves freezing the workpiece with liquid nitrogen or another cryogenic medium to make the burrs brittle. Once the burrs are frozen, they are removed by blasting the part with a high-velocity stream of abrasive particles or by mechanical agitation. Cryogenic deburring is effective for removing small burrs from plastic and rubber components, but it can also be applied to metal parts.
Laser Deburring
Laser deburring is a non-contact method that uses a focused laser beam in order to melt and vaporize burrs. This method is highly precise, so it’s perfect for delicate and intricate components that cannot tolerate mechanical stress.
It’s useful for micro-components or parts with complex shapes, where traditional methods might cause damage or be less effective.
Why Is Deburring Necessary?
Deburring is necessary as it helps ensure the safety, functionality, and longevity of your final product. Burrs can cause several problems, such as:
- Safety Hazards: Sharp edges and splinters from burrs can cause injuries to operators or end-users.
- Functional Issues: They can interfere with the fit and function of parts, leading to mechanical failures, especially in industries like automotive manufacturing where precision is crucial.
- Aesthetic Concerns: Burrs can take away from the visual appeal of a product, and customers will be unhappy.
- Increased Wear and Tear: Burrs can cause unnecessary friction and wear on moving parts, reducing the lifespan of components. This is particularly true for applications involving movement, such as in welding joints or rotating parts.
How Drawn Metal Can Help
Understanding what deburring is and why it is essential is key if you want to achieve high-quality results in metalworking. Burrs, though often small and seemingly insignificant, can have a significant impact on functionality, safety, and aesthetics of machined components.
If you have any queries about how we can help you, feel free to contact us. Likewise, if you know what metal materials you need, you can easily request a quote from us.
Contact Us Today!
Download our DMT Brochure
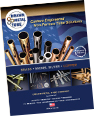