What Is Wire Drawing?
Definition of Wire Drawing
Wire drawing is a metalworking process that transforms thick rods or wires into thinner ones. It works by pulling the wire through a die, a shaped opening that reduces the cross-section. As the wire is pulled, it lengthens to maintain its original volume.
This technique has been around for centuries and has shaped the world around us in countless ways, from powering our cities to miniaturizing electronics. They are fundamental to modern infrastructure, communication, and everyday objects.
Historical Background of Wire Drawing
The exact origins of wire drawing are unclear, with evidence suggesting its use in Mesopotamia and ancient Egypt. However, it wasn't until the 14th century that wire drawing became a well-established craft in Europe. Initially, the process was done by hand, but advancements like water-powered draw benches in the 16th century revolutionized its efficiency.
Importance and Applications of Wire Drawing
Wire drawing is an essential industrial process with a vast range of applications. Here's a glimpse into the world shaped by wire drawing:
Overview of Wire Drawing Applications
From delicate wires in electronics to the massive cables that hold suspension bridges, wire drawing plays a vital role in countless industries.
Common Products Produced Using Wire Drawing
Copper wires for electrical wiring, steel cables for construction, springs in everything from machinery to toys, and even the strings for musical instruments are all products of wire drawing.
Principles and Techniques of Wire Drawing
There's more to wire drawing than just pulling metal through a hole. Here's a breakdown of the principles and techniques involved:
Basic Principles of Wire Drawing
The core principle of wire drawing is the conservation of mass. As the diameter of the wire reduces during wire drawing, the wire stretches to maintain its volume.
Additionally, the process strengthens the wire through work hardening, a phenomenon where the metal's internal structure is altered to resist deformation.
Overview of the Wire Drawing Process
The wire is first prepared with a tapered end to fit through the die. It's then pulled through the die by a wire drawing machine, reducing its diameter and increasing its length.
Modern machines are complex and may include multiple stages with dies of progressively smaller sizes. This allows for achieving significant diameter reductions without putting too much stress on the wire in any one pass.
Wire Drawing Machines and Equipment
Modern wire drawing machines are complex, with features like capstans (winches) for pulling, dies made from hard materials like tungsten carbide, and various lubricants to reduce friction during the wire drawing process.
These lubricants can be in the form of liquids, pastes, or even soap solutions, depending on the specific wire material and desired finish.
Different Types of Wire Drawing Processes
There are different variations of the wire drawing process that are used to achieve specific results. However, the core principle of pulling the wire through a die is always the same. Here are some of the common processes:
- Single-draft drawing: This is the most basic form of wire drawing, where the wire is pulled through a single die in one pass. It's suitable for achieving moderate reductions in diameter for larger wires.
- Multi-draft drawing: For achieving significant reductions in diameter, especially for finer wires, multi-draft drawing is employed. The wire is pulled through a series of dies with progressively smaller sizes in a single machine. This reduces the stress on the wire in each pass, preventing breakage.
- Wet drawing: For wet drawing, the wire and die are submerged in a lubricant bath during drawing. This is particularly useful for drawing softer metals or achieving a specific surface finish on the wire.
- Dry drawing: Dry drawing uses a dry lubricant, often in the form of a powder or a coating applied to the wire, to reduce friction. This method is faster than wet drawing but may not be suitable for all materials or applications.
- In-line annealing: For some metals, the work hardening caused by drawing can make it difficult to continue drawing without the risk of breakage. In-line annealing involves passing the wire through a heating zone within the drawing machine to soften it before further reduction. This allows for continuous multi-stage drawing processes for such materials.
These are just a few examples. However, the specific type of wire drawing process chosen will depend on the material being drawn, the desired final diameter, and the required properties of the finished wire.
Factors Affecting Wire Drawing
Several factors influence the success and outcome of the wire drawing process. For example, the type of metal being drawn can significantly impact the process. Here's a deeper look into the factors affecting wire drawing:
- Softer metals: Softer metals like aluminum or copper are more prone to breakage during drawing due to their lower tensile strength. To overcome this challenge, multi-stage drawing with smaller diameter reductions per pass is often used. Additionally, lubricants and techniques like wet drawing can help reduce friction and stress on the wire.
- Harder metals: Harder metals like steel or high-carbon steel require more force to pull through the die. This necessitates sturdier machinery and appropriate die materials like tungsten carbide to withstand the higher pressures. In some cases, pre-heating the wire before drawing can improve its workability.
- Heat generation: Friction during drawing can generate heat, which can soften the wire and make it more prone to breakage. Using proper lubricants and controlling the drawing speed can help minimize heat generation.
- Preheating for certain materials: For some metals, preheating before drawing can improve their workability. This can be especially beneficial for harder metals or when aiming for larger reductions in diameter per pass.
- Drawing speed: Higher drawing speeds can increase efficiency but also generate more heat. The optimal speed depends on the wire material, diameter reduction, and desired properties.
- Amount of reduction per pass: Larger reductions in diameter per pass put more stress on the wire and require more force. A balance needs to be struck between achieving the desired final diameter and avoiding breakage. Multi-stage drawing with smaller reductions per pass is often employed for finer wires or those made from more challenging materials.
Effect of Wire Material on Wire Drawing
The type of metal being drawn can significantly impact the process. Softer metals require specific techniques to prevent them from breaking during wire drawing.
Influence of Temperature on Wire Drawing
In some cases, controlling the temperature of the wire during drawing can improve the process and the final properties of the drawn wire.
Impact of Speeds and Reduction on Wire Drawing
The speed at which the wire is pulled and the amount of diameter reduction achieved in a single pass can affect the quality and properties of the drawn wire.
Role of Friction in Wire Drawing
Friction between the wire and the die can generate heat and affect the final properties of the drawn wire. Lubricants are used to minimize friction during the process.
Effect of Surface Finish on Wire Drawing
The initial surface finish of the wire can influence the final finish of the drawn wire. Special preparation techniques can be employed to achieve a desired surface finish.
Mechanical Properties of Wire after Drawing
Wire drawing can significantly alter the mechanical properties of the wire:
Changes in Mechanical Properties during Wire Drawing
Wire drawing typically strengthens the wire by a process called work hardening. It can also improve the wire's surface finish and dimensional accuracy.
Importance of Wire Diameter and Cross-Sectional Area
The final diameter and cross-sectional area of the drawn wire are crucial for its intended use. Wire drawing allows for precise control of these dimensions.
Influence of Wire Drawing on Wire's Electrical Conductivity
In some cases, wire drawing can slightly reduce the electrical conductivity of the wire. However, for most electrical applications, this reduction is negligible.
Impact of Wire Drawing on Wire's Tensile Strength
Wire drawing generally increases the tensile strength of the wire, making it more resistant to pulling forces.
Challenges and Advancements in Wire Drawing
While seemingly straightforward, wire drawing presents its own set of challenges. Here are some areas where advancements are being made:
Issues with Drawing Soft Metals
As mentioned earlier, softer metals require special techniques to prevent them from breaking during wire drawing. Researchers are constantly developing new methods to overcome this challenge.
Reduction Techniques for Wire Drawing
Multi-stage drawing with progressively smaller dies helps achieve significant reductions in diameter without damaging the wire. Advancements in die design and materials are further improving this process.
Enhancing Surface Finish in Wire Drawing
New lubricants and surface preparation methods are constantly being developed to improve the final finish of the drawn wire. This is crucial for applications where a smooth, blemish-free surface is essential.
Innovations in Wire Drawing Technology
Advancements in automation, monitoring systems, and even the use of lasers for wire drawing are shaping the future of this industry. These innovations improve efficiency, consistency, and the ability to produce even finer wires.
How can Drawn Metal help you
At Drawn Metal, exceptional quality and service is at the heart of our business. We have plenty of skilled professionals on hand to help to ensure you get exactly what you need.
Whether you require wire drawing for automotive components, the high-strength demands of construction projects, or any other niche requirements, our commitment to quality and customer satisfaction is of utmost importance. If you have any questions, feel free to contact us.
Contact Us Today!
Download our DMT Brochure
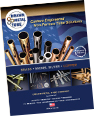